Air compressing with the Wing'd
mills
1.Simultaneous air compressing to same pressure at the
windmill as the pumped water
When the Wing'd mills are pumping water a distance
horizontally either ashore and/or overland, it reduces the flow friction in
the pipeline to smoothout the pump pulses with an air cushion. The main
complication with standard air chambers is the loss of air by absorption
into the pressurised water, which requires airbags or diaphraghms or manual
replenishment.The Flo’Pump has an inlet
at the waterline top of the cylinder that snifts in air behind the piston weight falling through the water to
automatically replenish the built-in
air and valve chamber above the
cylinder. Excess compressed air can be tapped for a secondary use, normally
aeration of the pond bottom. If the Flutterwell
is also pumping through a pipeline a snifter valve below a check valve
entry into a simple bag-less air chamber at the wellhead snifts air as the watercolumn regresses on the
downstroke of the PipePump. This gives output
air to water in a 1/3 nominal (atmospheric) ratio.
2. Dedicated Air Compressing with additional battery
charging
This design is based on the Honda 50cc motorcycle engine
Its standard tierod cylinder and head mounting makes it easy to extend the
cylinder with the high pressure (HP) valve head, and then a cored block for
the small diameter high pressure cylinder, then a normal block for the LP
cylinder and finally the LP head. The most difficult part is attaching the
extension piston rods to the top of the original delicate aluminum piston.
(sans oil rings).
The HP and LP pistons are interconnected by a central rod and used the
standard cup seals. However the cup dead space was filled with plastic plug
to minimise the knocking and jamming from minor bottoming out for the
efiiceint minimum dead air space. The cam chain is rerouted to directly
drive the engine oil pump and an oil path created to the high side of the
top LP cylinder just under the cup lip BDC.
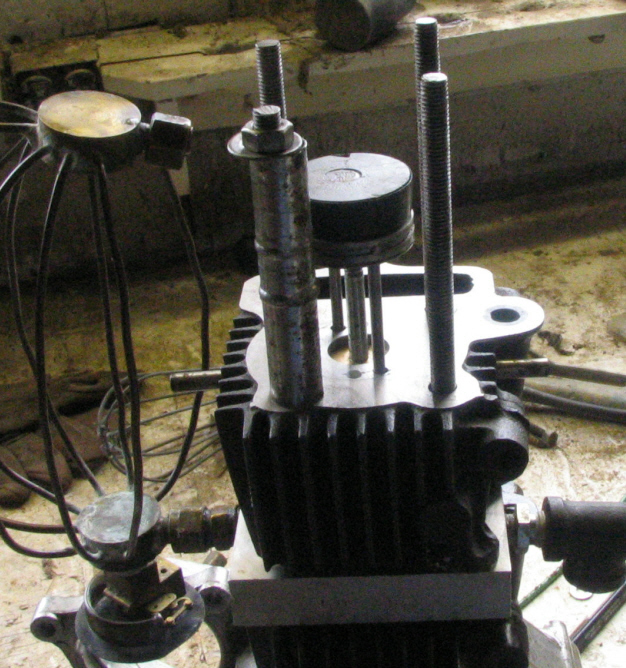
The previous experience was that standard compressor reed valves had to
be adjusted most carefully to minimise high static leaking. Presumably they
are demanded by the high rpms and temperature buildup of standard
compressors. Here with intermittent operation at lower peak rpm and the
certainty of good cooling in the wind, and finally the intercooling, the
temperature should stay below 300F and the tolerance of high temperature if
not standard O-ring seals. These were used on the seats of all 4 valves, 3
of which were sprung brass sliders in the solid aluminum heads with only
the input HP valve remaining as a leaf
because of space constraints.
The cylinders were separately bench tested and these valves developed to
achieve very low static leaking. Nonetheless in the assembled unit the
Intercooler loses static pressure to the engine space by leaking around the
HP piston cup. To minimise this loss of air in intermittent operation the
intercooler has to be optimised for high heat transfer but low internal
volume and low flow friction using parallel connection of several fine bore
copper tubes. The standard crankshaft seal in the engine will not stand
significant pressurisation.
In 2005 an alternator was tested directly connected to
this stub of the crankshaft and heavy pulses of current delivered at 12v
with no additional noise. In fact the principal noise are the compressor
strokes, so proving that even a spur gear train in an enclosed oil bath is
much quieter than the previous external ring gear driving a ratcheting
pinion on the alternator. However now the alternator inertia is tapped by
the main compressor load as well, so the alternator delivered voltage and
power are both reduced. Without electronic load switching and just ordinary
voltage regulation, an alternator is a constant power load and so cannot be
primary for the Wing'd Mills.
|